Die Coater
A die coater is also basically a closed coating method and it has the advantage of coating stability, allowing for ultra-high precision coating.
There are significant variations in the wetting methods and edge shapes for a die coater, which must be determined according to the resin being applied, the substrate and the coating thickness. Depending on the fluid characteristics, it is also necessary to achieve optimal conditions including the internal shape.
To determine a die method, it is desirable in most cases to perform not only simulations but verification tests using the actual coating fluid.
Introducing Die Coater
Slot Die
In this method, a film is formed using a gap introduced between the die and the substrate on the back roll. Suitable for medium to high viscosity, for producing medium thickness coating. It is also suitable for intermittent patterned coating.
Features
High precision coating, allows for intermittent patterned coating, high coating quality, and good stability
- Reference range of application
- Coating speed:1~200m/min
- Viscosity:100~50000mPa・s
- Coating amount:10~1000μm・Wet
- Use examples:Battery electrodes, adhesives, electronic materials, etc.
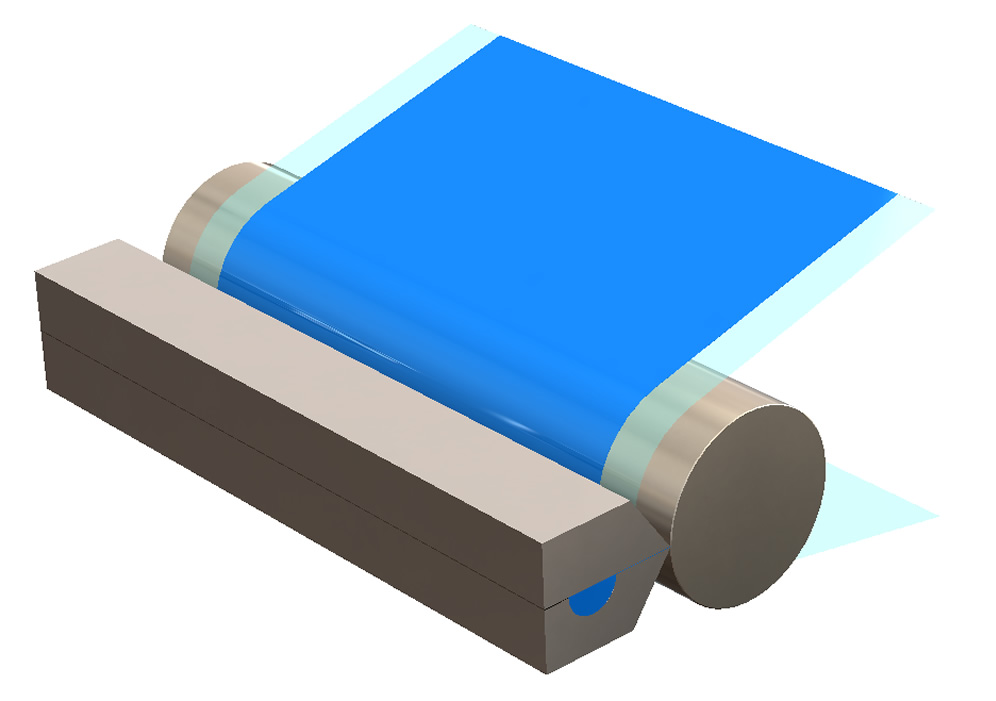
DV Die
In this method, a film is formed using a vacuum box introduced in the upper stream of the die, aiming at suppression of air entrainment and bead stabilization. This method has a wide range of applications, from thin to thick coating, but it is mostly used in low viscosity thin coating in the gravure field.
Features
High precision coating, low viscosity thin coating, high coating quality, good stability, low dependence on gap precision
- Reference range of application
- Coating speed:1~150m/min
- Viscosity:1~5000mPa・s
- Coating amount:1~200μm・Wet
- Use examples:Functional materials including optical use, adhesives, electronic materials, etc.
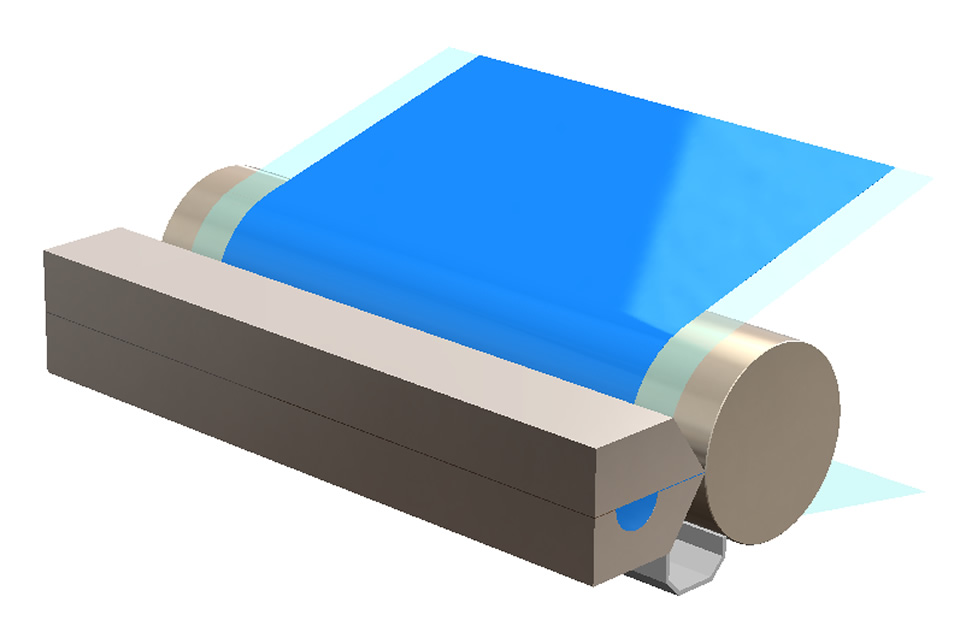
R&R (R2)
This is one of the tensioned-web die methods without back roll. This allows for high speed and thin coating. The substrate, resin, and running conditions greatly influence the performance achieved using this method.
Features
Thin coating, high precision high coating, coating quality, good continuous stability
- Reference range of application
- Coating speed:5~500m/min
- Viscosity:1~1000mPa・s
- Coating amount:1~30μm・Wet
- Use examples:Optical materials, electronic materials (MLCC), Hard coatings, Separators for electrodes.
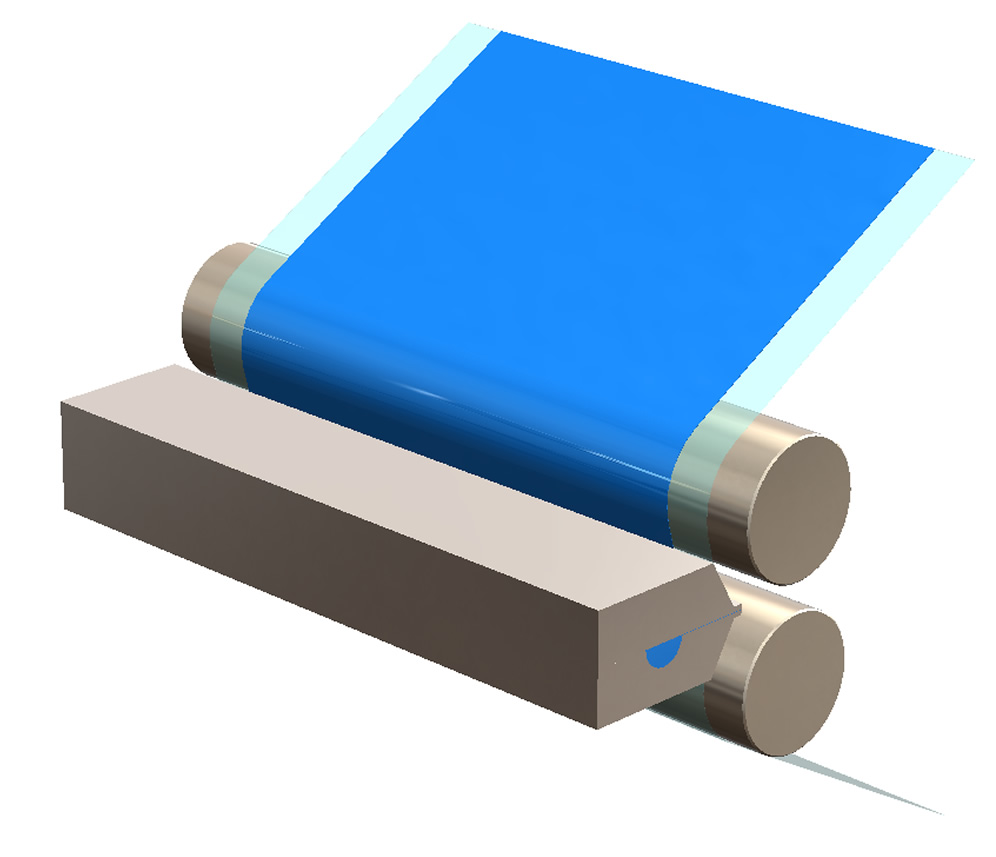
Multi-layered Die
For the purpose of enhancing the production efficiency and improving the functionality, this method makes it possible to form multiple layers at the same time using wet coating.
Matching of the resin conditions is a prerequisite for using multi-layer methods.
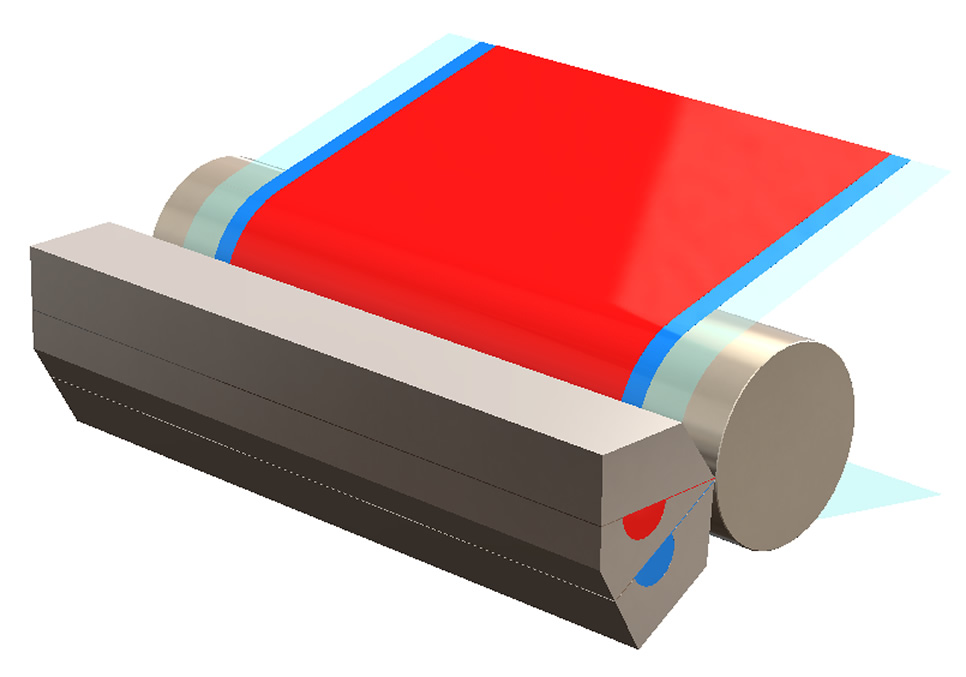
Simultaneous Double Face Die
Two dies are positioned on the both sides of the substrate, one on the front side and the other on the back side, allowing coating films to be formed on both sides of the substrate. This leads to increased production efficiency, but it depends greatly on the substrate, resin and drying conditions. There are several patterns for die positioning, depending on the arrangements of the drying machine used after the coating process, and also on the substrates to be used.
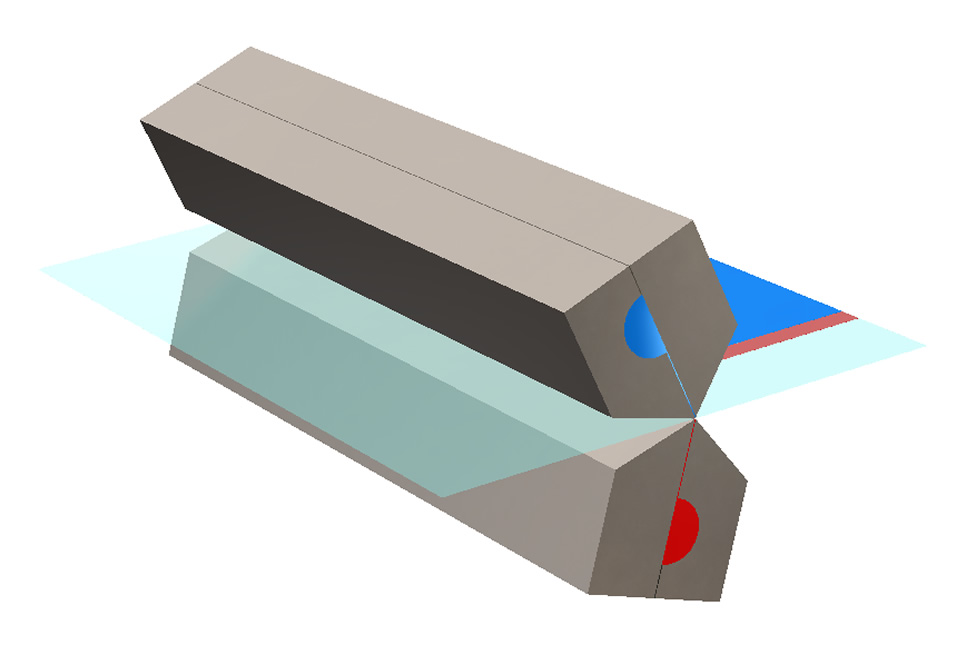
Inquiry
To find more about HIRANO TECSEED coaters, dryers, and other peripheral equipment, contact us using the form below.